Buy and sell Nickel. Buy Nickel online
Nickel (Ni) is a chemical element with an atomic number of 28 and is placed in group 10 of the periodic table. It is a silvery-white transition metal with a slight golden tinge and is abundant in the earth’s crust. It is found in the earth’s interior, mainly in the core and in various minerals or meteorites. Nickel is mainly used in stainless steel and in the formation of other alloys that are resistant to corrosion. The largest producers of nickel are the following: Indonesia, New Caledonia, the Philippines, Australia, China, Canada and Russia.
Nickel recycling
Nickel can be recycled without any loss of quality, which is why it is so important to recycle it. When this metal is recycled, its second life is mainly as stainless steel and also as carbon steel. Even so, a large amount of the metal is still not recycle.
Find out the price of nickel per tonne
Discover the price of nickel per tonne according to the LME in both USD and EUR. In this section designed for professionals in the recycling sector you will be able to see the price movements of nickel scrap and other metals.
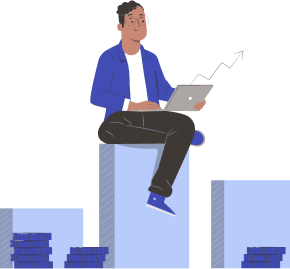
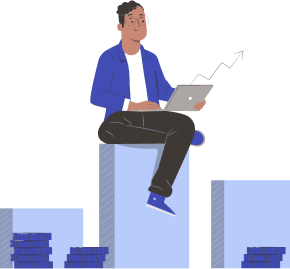
Contacta con nosotros
¡Descubre ScrapAd de la mano de nuestro equipo!
Te enseñaremos las ventajas del marketplace y te guiaremos en su uso para despejar todas tus dudas.
Thank you!
Our team will contact you as soon as possible.
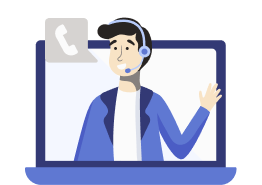
Error
An error has occurred. Please try again later.