What is metal smelting and what are its types?
In the world of industry, especially in scrap, smelting plays a crucial role. In this article, we will explore smelting, what it is, its types and how it is related to metals and the waste recovery process.
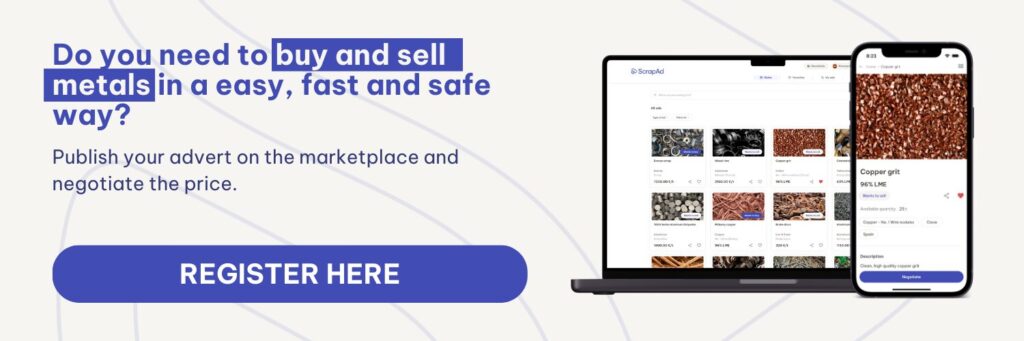
What is smelting?
Smelting is a 6,000-year-old industrial molding process that involves melting a solid material to shape it into a liquid that will be used to fill a mold and create a desired part or product. In the metalworking industry, this process varies depending on the type of metals and types of scrap metal used to produce a wide variety of objects. Some parts can only be made by casting, as they are not suitable for other processes such as forging or welding. The choice of smelting method depends on the composition of the metal and its fluidity.
Metal smelting is an essential part of the value chain in industry, to the extent that, there are recycling trade fairs worldwide such as the Euroguss, where they deal exclusively with all issues related to the function, from technological advances to production improvements for the reuse of valuable materials.
Types of smelting
There are several types of smelting in the field of metallurgy, each adapted to different needs and applications. We have complied some of the most common:
Smelting in sand
Sand smelting is a versatile process used to cast metal alloys, both ferrous and non-ferrous. It is widely used in the mass production of metal parts such as engine blocks, cylinder heads and crankshafts for automobiles. In this process, use is made of a mold made of silica-based materials, such as natural or synthetic sand, which creates the mold surface in two parts: the lid (upper part) and the drag (lower part). The molten metal is poured into a pattern through a pouring cup and allowed to cool to take the desired shape. Excess metal is then removed to obtain the final melting product.
Advantages include its relative low cost, the ability to manufacture large parts and its suitability for metals with high melting points, such as steel and titanium. On the other hand, it has some disadvantages, such as lower precision compared to other methods, limitations in manufacturing parts with specific dimensions, and a rough surface finish on the resulting products.
Centrifugal smelting
Centrifugal smelting, also known as rotary melting, is a process where molten metal is poured into a preheated rotating mold, and centrifugal forces distribute the liquid at high pressure inside the mold.
There are three variations to this process:
- True centrifugal smelting: makes the metal stick to the sides of the mold due to continuous rotation.
- Semi-centrifugal smelting: completely fill the mold using a trough.
- Vertical centrifugal smelting: uses directional molding following the same process as true centrifugal casting.
The advantages of this process include better yield and less scrap, high density and few defects in the meltings, as well as its suitability for manufacturing barrel and jacket composite metal parts without requiring gates or elevators. Some of the disadvantages are the need for significant investment, the requirement of skilled labor and the limitation in the production of specific shapes.
Die smelting
In this process of smelting metals such as zinc, tin, copper and aluminum, they are injected at high pressure into a previously lubricated reusable mold. The pressure stays high during rapid injection to prevent the metal from hardening. After the process, the parts are removed and finished to remove any excess material.
There are two types of die smelting based on the pressure used:
- Low pressure smelting: used when it comes to larger and simpler parts.
- High pressure smelting: to produce large quantities of parts with complicated geometries.
The advantages of die smelting include high precision and dimensional tolerance, less need for further machining, rapid cooling of the molten metal and ability to run for more hours without needing to replace the die. Some disadvantages are relatively high tool costs and difficulty in ensuring mechanical properties on parts.
Vacuum die smelting
Vacuum smelting is a process in which liquid metal is poured into the mold inside a vacuum chamber to eliminate bubbles and air pockets. By evacuating the air from the mold cavity, the possibility of trapping gases during metal injection is reduced. The metal is then solidified in a heating chamber and removed from the mold. This method of vacuum smelting is used in industries such as automotive, aerospace, electronics, marine and telecommunications, among others.
The advantages of vacuum smelting include the reduction of porosity, improvements in mechanical properties, the possibility of producing thin wall parts, the ability to perform welds and thermal treatments. Some disadvantages are the high cost of the tools, the short life of the mold used and possible problems related to the vacuum.
Investment smelting
Investment smelting, also known as investment smelting, is a process that involves creating a disposable ceramic mold around a wax pattern, then removing the wax and pouring molten metal into the mold to create metal parts. This method is used in the production of metal castings such as gears, bicycle trunks, motorcycle discs and machinery parts.
The advantages of investment casting include the ability to produce thin-walled parts with high surface quality, the ability to smelt difficult alloys such as stainless steel, and the ability to create parts with 90-degree angles. However, some disadvantages are that this process is labor intensive, has a longer production cycle and involves higher mold making costs since a new wax pattern is needed for each casting cycle.
Relation between metal smelting and recyclable waste
In summary, smelting is an essential process in the metals industry. It transforms materials into valuable products and contributes to the reuse of resources, which in turn helps to raise awareness of the importance of industrial recycling. On our platform, we provide opportunities to buy and sell scrap and metals that can undergo this smelting process.
On ScrapAd, companies in the recycling sector can buy and sell metals, easily, quickly and safely. Thus, we give a new opportunity to these wastes to return to the production flow, even polluting waste, so they do not end up in the landfill. Sign up for free and find out what we can do for you and the planet.